The Thermoplastic Extrusion Process at Spring Lake
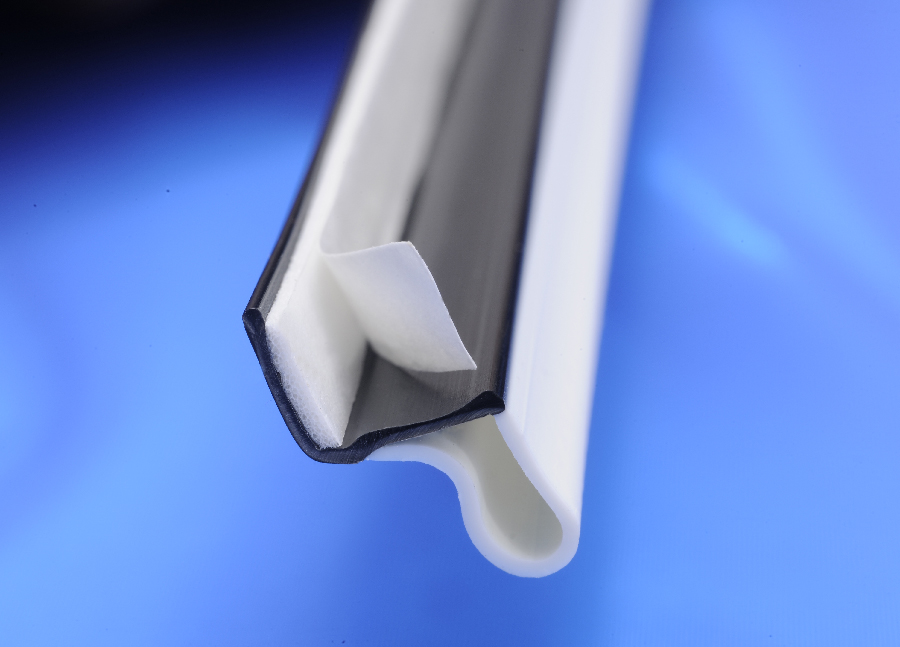
Thermoplastic components are generally manufactured using one of two industrial processes. The first being injection molding, where molten plastic is injected under high pressure into a mold, and hardens into the desired shape as it cools. The second being extrusion, where molten plastic is pushed through a die to form a continuous shape and then it’s cut to the desired length.
At the Cooper Standard ISG Spring Lake facility, we specialize in plastic extrusion. I’ve noticed a greater familiarity with the injection molding process in this region, so when visitors tour our facility and see an extrusion line for the first time, they are often very intrigued as they watch and witness how different the equipment and processes are. The hot profile passing through the water trough and the punching and laser etching processes are particularly fascinating to people. The automation of multiple processes in a single line is not widely known, making it uncommon for people to be familiar with such operations.
Inn a lot of ways, even though I’ve been doing this a long time, I’m constantly reminded about how interesting plastic extrusion is.
The Extrusion Process
Extrusion involves pushing molten material through a shaped opening, similar to Play-Doh or toothpaste coming out of a tube. That’s the basic idea, but of course it’s a little bit more sophisticated when we’re making a specialized product like a thermoplastic seal or component.
In thermoplastic extrusion, a custom die shapes the product, crucial for long-term quality. It's far more intricate than a toothpaste tube opening.
Our in-house tooling shop gives us a competitive edge by creating Extrusion tooling internally, enhancing accuracy and speeding up production significantly through direct collaboration between engineers and toolmakers.
Once the die is mounted on the extruder, various thermoplastic materials can be fed from a hopper, including TPV, polypropylene and PVC, with a wide range of durometers from a very soft flexible to a rigid material. How an extruder melts the thermoplastic Single-screw extruders use a rotating screw inside a heated barrel to melt plastic pellets through shear/friction and conduction. Consistent melt is critical for Extrusion consistency. Our Extruders range in size from 1 ¼ to 3 ½ inch diameter, across our 19 Extrusion lines, this gives us the ability to extrude thermoplastic components in a wide range of sizes.
Before reaching the die, the molten plastic passes through mesh screens of different fine levels ranging from 20 to 200 mesh. This process helps ensure a consistent blend, filters contaminants, builds back pressure and prepares the material for shaping through the die.
The shaped material exits the die and passes through a cooling environment, utilizing air tables or water tanks ranging from 8 to 30 feet in length to regulate speed. Sizing the extrusion controls shrinkage and maintains dimensions during cooling, often aided by precision vacuum and water Calibration/Sizing for precise tolerances. Finally, the extrusion is cut to desired lengths using an inline saw, fly knife cutter, guillotine-style cutter or punch press to produce individual components.
For intricate or multiple durometer parts, we can operate up to three extruders on a single line, requiring thorough planning and internal engineering skills. This method is highly effective, efficient, and cost-effective for manufacturing.
The plastic profile moves down the line at a precise speed, translating to high production rates ranging from dozens to thousands of pieces per hour. Various value-added processes can be integrated into the extrusion line, such as punching holes, applying tapes, printing or laser etching, enhancing efficiency and reducing post-shipment tasks for customers. Approximately, half of the parts are shipped ready for installation, while others undergo additional offline operations like tabbing, punching, assembly or cutting using robotic cells equipped with advanced tools for intricate shapes and challenging angles, providing significant time and cost savings for customers.
Flexible extrusion lines
Our 21 extrusion lines position us as a larger extrusion facility. While 2-3 lines are dedicated to high volume parts for specific customers, the remaining lines are versatile, allowing quick transitions to produce various products for different industries. Operating on a “high mix, low volume” model caters to industrial customers’ needs for diverse parts with shorter lead times.
If you want to learn more about thermoplastic extrusion and how we can manufacture seals and components for you, give us a call anytime and let’s get the ball rolling.